ADVANTAGES OF ENSORCIA’S GROUP TECHNOLOGY
Science & Development
The main advantages of the IBAT Technology chosen by ENSORCIA, who has its worldwide license exclusive for Chile and Argentina, are related to its composition based on separation of the plants:
- the DLE extraction totally mobile located in the salt flat itself extracting and re-injecting brine;
- and other plants (carbonate, hydroxide) out of the salt flats and protected areas.
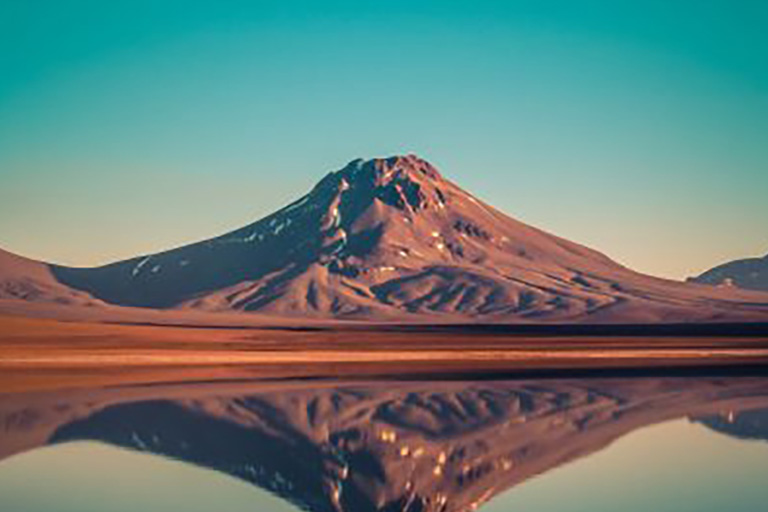
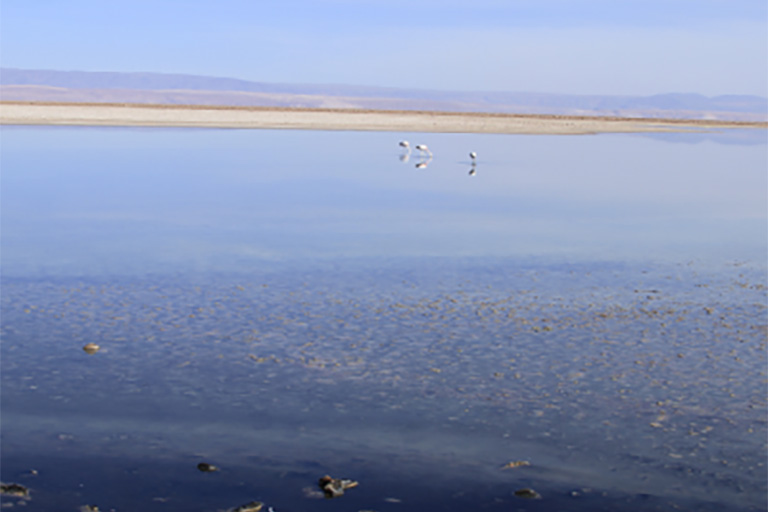
Selective absorption: During selective absorption, only chlorine and lithium are absorbed by the processing plant. The brine passes through the system separating the lithium chloride, returning up to 98% of the washed brine back to the salt.
A freshwater cycle rinses the lithium and subsequent steps increase the lithium chloride concentration to 35% to 40%.
The technology has been proven over the past 20 years with very good results. As it is, Dr. John Burba has made substantial improvements to his innovation, making the plant more efficient, fully modular, using a very small portion of land in the salt flat, having practically no impact on the environment, thus being able to access any salt flat regardless of its extension.
From traditional to a revolutionary performant and environmentally friendly solution with our licensed DLE technology
Our solution is the answer to this problem
As a way to solve this situation, in 1992 Dr. John Burba created and patented the technology known as “Selective Absorption”, which was implemented between 1994 and 1998 in northern Argentina and continues to be used successfully for more than 20 years and has been perfected over time.
The technology used by ENSORCIA Minerals and created by Dr. Burba, is characterized because it uses selective absorption to recover lithium chloride from high salinity brines. The resulting residual brine, with all its contaminants, such as magnesium and calcium among others, is re-injected into the salt flat, not producing any type of rejection on the surface of the salt flat, nor does it contaminate the brines in any way by re-injecting them with the same chemical composition that was extracted at the beginning of the production process.
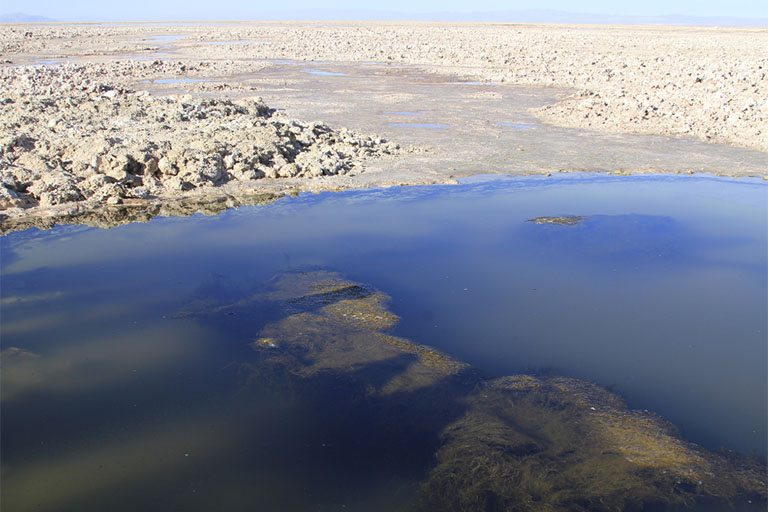
Mobile Modular DLE Plant
The first part of the plant is composed of DLE mobile units and support equipment, such as LNG tanks and water tanks that we bring in from outside (we do not use the existing water in the salt flat or surrounding areas). The mobile plants pump brine to the surface, which allows us to extract a 35% to 40% Lithium chloride solution through a chemical process. In parallel to this process, 90% of the extracted brine is re-injected into the salt flat with all its original minerals -such as magnesium, boron and calcium, among others- adding only 3 liters per second of industrial water for a production of 20,000 tons of lithium carbonate (Li2CO3) equivalent produced, thus preserving its water levels. As noted above, the entire process does not use water from local communities, but is transported from outside.
One of the main benefits of using this mobile technology is that it allows the extraction of Lithium chloride in small salt flats, with even low concentrations of lithium in their brines, which before these technologies, was economically unfeasible.
All this allows ENSORCIA Group to produce the first part in the salar with practically zero environmental impact. As it is installed on mobile elements, once the operation comes to an end, these elements are easily removed, leaving the salt flat in the same conditions as before the start of the operation, without affecting the flora and fauna of the place, nor the surrounding communities, preserving the salt flat for future generations to enjoy them.
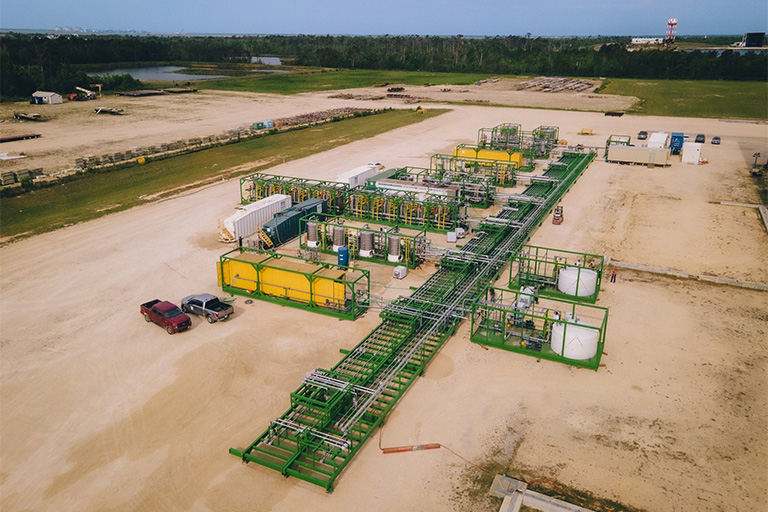
Fixed plant
INNOVATIVE TECHNOLOGY OF ENSORCIA Group
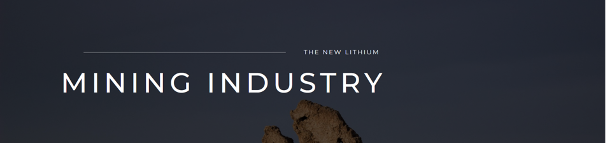
Overview of lithium mining
Lithium is currently produced mainly in five countries: Australia (from ores such as spodumene), Chile (brine), Argentina (brine), China (ores and brine) and the United States (brines). Chile supplies about 22% of the world’s lithium. As with any mining operation, lithium mining has a significant impact on the environment. Every time a company wants to start a large-scale mining operation, whether metallic or non-metallic mining, there is an environmental impact and a great concern from the communities near the mining area, not only because of the different pollutant that the mining industry normally spews, but also because of the increasing consumption of water and electricity. In most developed countries, including several European countries such as Norway, Germany and the United Kingdom, have announced that by 2025 and 2030 only electric buses and cars will be able to travel in their cities.
China has also declared something similar, as its main goal is to have all public transport buses powered by electricity in major cities. We can say that most countries today are trying in one way or another to become as independent as possible from fossil fuels in favor of alternative fuels and electric cars, this being one of the most important reasons for the rapid growth that the lithium industry is experiencing today, not only in mining, but also in the production of more efficient batteries for various uses.
We can affirm that most countries today are trying in one way or another to become as independent as possible from fossil fuels in favor of alternative fuels and electric cars, this being one of the most important reasons for the rapid growth that the lithium industry is experiencing today, not only in mining, but also in the production of more efficient batteries for electric vehicles.
The key to the technology behind electromobility is the lithium-ion battery, which is made up of thousands of units called “electrochemical cells”, These in turn are composed of a lithium cathode of the LNCA (lithium-nickel-cobalt-aluminum) or LNMC (lithium-nickel-manganese-cobalt) type, an anode generally made of graphite (natural or synthetic), an electrolyte (consisting of a lithium salt and an organic solvent) and a plastic separator. The voltage of this unit electrochemical cell is currently between 3.6 and 4.5 volts. The lithium consumption in a lithium-ion battery expressed as lithium carbonate equivalent (LCE) is currently between 0.75 and 0.8 kg per kWh. Therefore, a 70 kWh battery (typical of Tesla for its Model S car) will consume between 53 to 56 kg of Li2C03 battery grade.